How to make your edges look great
When glass touches fiber, sometimes it sticks. This can produce wicked little spikes or a ruffled edge that isn’t very pleasing. There are many ways to avoid this; we’ll look at some of them here.
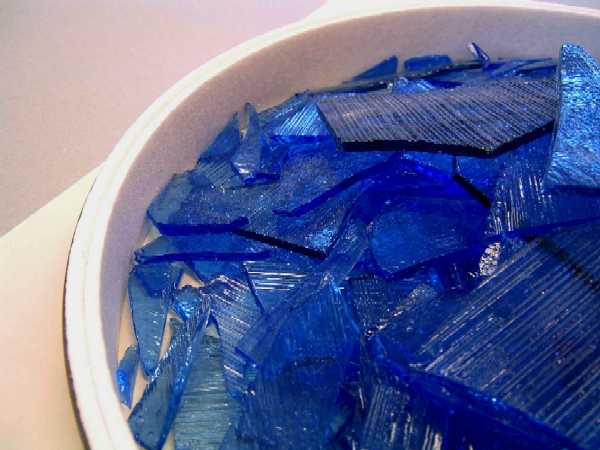
Pile the glass. If you’re making a casting with frit or scrap, you can avoid nasty edges by moving your glass away from the fiber before firing. When the glass melts, it flows to meet the fiber, making a nice rounded edge. For this technique to work, you must use enough glass to create a flow (usually more than 3/8” thick,) and give the glass enough time at temperature to allow it to flow into place.
Shelf paper. Adding a layer of shelf paper (like Bullseye Thinfire) between the fiber and glass can create a smooth, almost polished edge. When using this technique, the shelf paper should be close to your expected glass thickness; taller paper can flop into the glass during firing.
Shelf primer. Painting the inner surface of your fiber with a layer of shelf primer can yield nice smooth edges. This helps extend the life of your fiber, too.
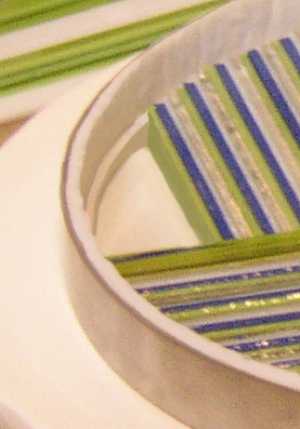
Stepped fiber. With designs that are initially dense (like strip bowls or other sheet-centric designs) trimming your inner layer of fiber to be slightly lower than your expected thickness will cause the glass edge to roll down to meet the fiber, making a nice rounded edge. Always use a second layer of full-height fiber, though.
Remove a fiber layer. Make a piece using two or more layers of fiber at the edge. Remove the innermost layer of fiber after the first firing, and fire again using the same profile. During the second firing, the glass will flow out to meet the exposed fiber layer, making a nicely rounded edge.
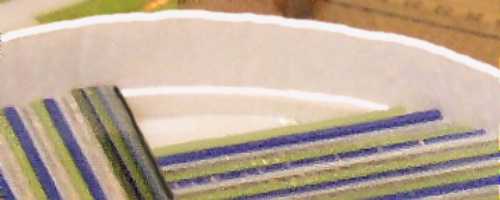